How Factory Audits Improve Product Quality
How Factory Audits Can Improve the Product Quality?
Are you looking to verify the reliability and competence of your suppliers before integrating them into your supply chain?
Factory audits offer a comprehensive assessment of your supplier’s sourcing and operational practices, ensuring alignment with your company’s brand identity. These types of audits are also instrumental in ensuring compliance, quality control, and ethical practices within manufacturing facilities. Factory audits are tailored to specific areas of concern and industry requirements. Here are the six most common types of factory audits:
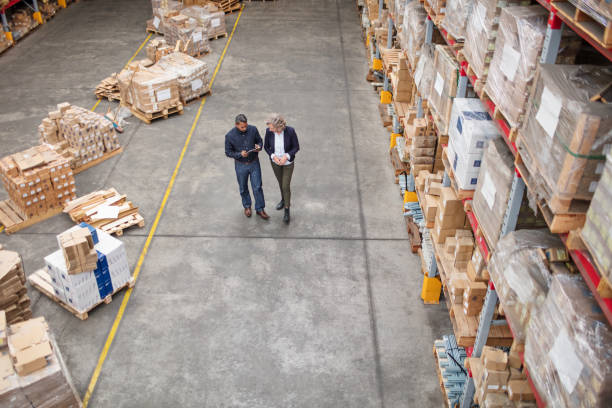
1. Compliance Audits
Compliance audits focus on ensuring that a manufacturing facility adheres to local and international regulations relevant to its industry. These audits confirm that the facility operates within the legal framework, minimizing the risk of legal complications.
- Ensures adherence to industry regulations.
- Minimizes legal risks and potential fines.
- Builds trust with regulatory authorities.
- Demonstrates commitment to ethical business practices.
- Helps identify areas for process improvement.
- Enhances overall operational efficiency.
2. Ethical Audits
Ethical audits assess the ethical standards and practices within a manufacturing facility. They evaluate labor practices, fair treatment of workers, and adherence to international ethical standards. As one of the eminent types of factory audits, ethical audits are crucial for businesses aiming to maintain responsible supply chains.
- Validates fair treatment of workers.
- Fosters responsible supply chain management.
- Improves brand reputation and customer trust.
- Mitigates risks of labor disputes and controversies.
- Encourages ethical behavior in business partners.
- Demonstrates corporate social responsibility.
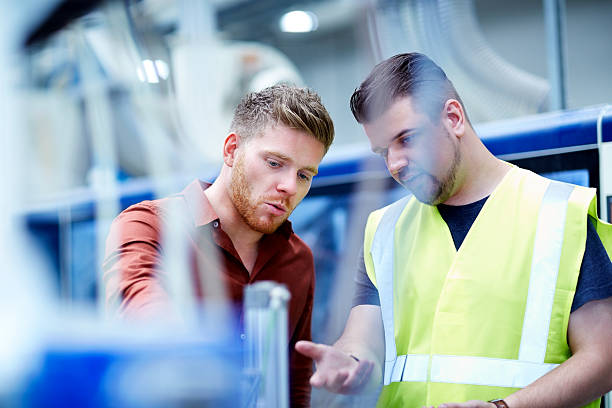
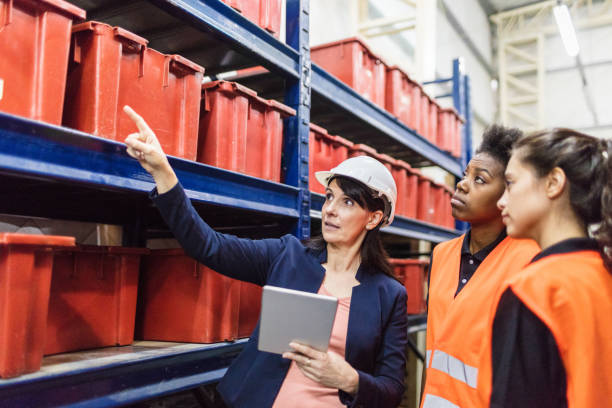
3. Quality Control Audits
Quality control audits are dedicated to evaluating a facility’s quality control systems. They assess processes, procedures, and standards to ensure that products consistently meet predefined quality benchmarks. Quality control audits are essential for maintaining product excellence.
- Maintains consistent product quality.
- Reduces defects and product recalls.
- Enhances customer satisfaction and loyalty.
- Identifies opportunities for process optimization.
- Ensures compliance with quality standards.
- Boosts competitiveness in the market.
4. Environmental Audits
Environmental audits focus on a facility’s environmental practices and their compliance with environmental regulations. They assess waste management, resource usage, emissions, and sustainability initiatives. Environmental audits contribute to responsible manufacturing.
- Promotes sustainable manufacturing practices.
- Reduces environmental impact and resource waste.
- Helps meet environmental regulations and standards.
- Demonstrates commitment to corporate sustainability.
- Enhances brand reputation as an eco-friendly company.
- Identifies cost-saving opportunities through resource efficiency.
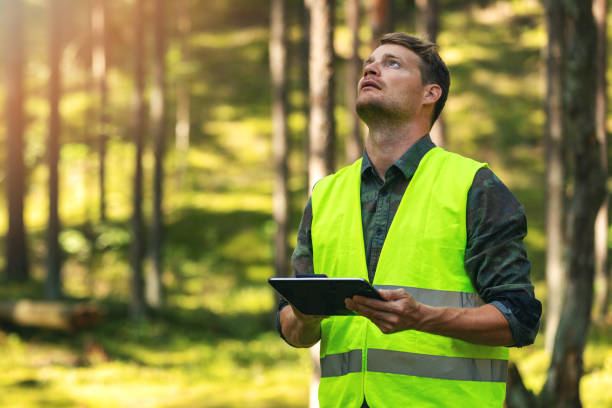
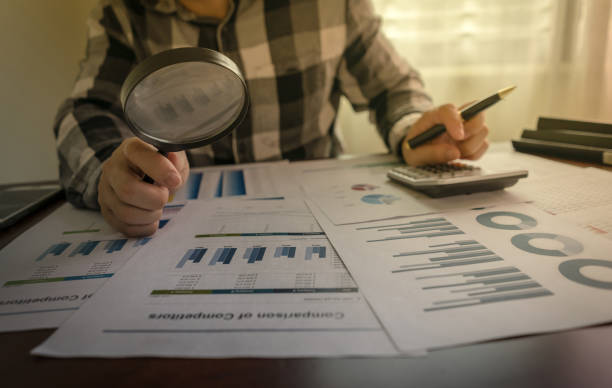
5. Social Responsibility Audits
Social responsibility audits evaluate a facility’s commitment to social and community welfare. They examine corporate social responsibility practices, philanthropic efforts, and contributions to the well-being of the community.
- Validates corporate commitment to social welfare.
- Builds positive relationships with local communities.
- Attracts socially conscious consumers and investors.
- Demonstrates ethical business practices.
- Strengthens corporate reputation and trust.
- Fosters employee engagement and pride.
6. Security Audits
Security audits assess the security measures in place within a manufacturing facility. They evaluate security protocols, access controls, data protection, and risk management to safeguard against security threats.
- Enhances facility security and asset protection.
- Ensures data confidentiality and privacy.
- Identifies vulnerabilities and security gaps.
- Mitigates risks of security breaches and cyberattacks.
- Demonstrates commitment to safeguarding sensitive information.
- Enhances trust and confidence among stakeholders.
Each type of factory audit serves a specific purpose, ensuring that manufacturing facilities operate ethically, compliantly, and with a focus on quality and safety. The choice of audit type depends on the industry, business goals, and areas of concern.
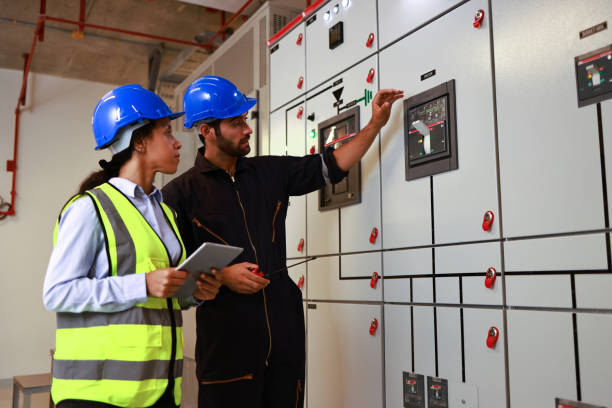
Product Inspection: The Final Quality Check
Product inspection is a critical component of quality control in manufacturing. It involves the systematic examination of products at various stages of production to ensure they meet predefined quality standards. There are several types of product inspection, each tailored to specific needs:
While factory audits provide a holistic view of a manufacturing facility’s capabilities, product inspection focuses on the final quality check of individual products.
Pre-production Inspection (PPI): Conducted before production begins, PPI identifies potential issues, ensuring a smooth manufacturing process.
- Identifies potential issues before production.
- Prevents costly defects and delays.
- Ensures adherence to quality standards.
- Enhances overall production efficiency.
- Provides early corrective measures.
- Boosts confidence in production planning.
During Production Inspection (DPI): DPI monitors production in real-time, addressing problems promptly to maintain quality and efficiency.
- Monitors production progress and quality.
- Identifies and addresses issues promptly.
- Prevents defects from reaching final production.
- Enhances process control and efficiency.
- Maintains product consistency.
- Ensures adherence to production schedule.
Pre-shipment Inspection (PSI): PSI guarantees product quality before shipment, reducing the risk of defects reaching customers.
- Guarantees product quality before shipment.
- Reduces the risk of customer complaints and returns.
- Validates product compliance with specifications.
- Provides confidence in product acceptance.
- Mitigates risks in the final stage of production.
- Enhances customer satisfaction and trust.
Container Loading Inspection (CLI): CLI ensures goods are properly loaded for shipment, minimizing damage and errors during transit.
- Ensures accurate loading of goods for shipment.
- Prevents damage and loss during transit.
- Validates proper packaging and labeling.
- Confirms order quantities and contents.
- Reduces shipping errors and disputes.
- Enhances supply chain reliability.
Production Monitoring: This involves continuous oversight of production, allowing for quick problem-solving and adherence to quality standards.
- Offers real-time oversight of production.
- Identifies deviations and inefficiencies.
- Enables proactive problem-solving.
- Ensures adherence to quality standards.
- Facilitates timely decision-making.
- Improves overall production quality.
Sample Testing: Sample testing involves subjecting a representative subset of products to rigorous evaluation, ensuring they meet safety, performance, and quality standards. It provides valuable insights into product quality and compliance.
- Validates product performance and safety.
- Confirms compliance with industry standards.
- Identifies potential defects or issues.
- Prevents costly recalls and legal complications.
- Assures product quality to consumers.
- Enhances brand reputation and trust.
Each type of product inspection plays a crucial role in maintaining product quality, preventing defects, and ensuring customer satisfaction, ultimately contributing to business success.
In conclusion, factory audits and production inspections are invaluable tools in the pursuit of manufacturing excellence. Factory audits instill compliance, ethics, and quality at the core of operations, safeguarding businesses against legal risks and upholding brand integrity. Meanwhile, production inspections serve as the final quality checkpoint, ensuring products meet or exceed customer expectations, fostering trust and loyalty. Both processes are integral to enhancing efficiency, reducing defects, and securing a competitive edge in the global market. By prioritizing these practices, businesses not only protect their interests but also elevate product quality, customer satisfaction, and their reputation in the industry.