The Role of Quality Control in Supply Chain Management
The Role of Quality Control in Supply Chain Management
In today’s globalized and highly competitive business landscape, supply chain management is a critical aspect of any successful organization or manufacturing industry. The efficiency and effectiveness of the supply chain directly impacts a company’s ability to meet customer demands, reduce costs, and maintain a competitive edge. If we talk about the function of quality control in supply chain management, then nobody can deny the fact that quality control plays a pivotal role in ensuring products and services meet the desired standards, regulatory requirements, and customer expectations. In this blog, we will explore the multifaceted role of quality control in supply chain management and its far-reaching implications for businesses.
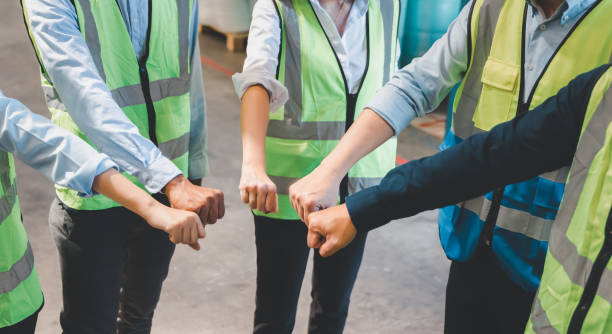
Quality Control and Supply Chain Management: A Perfect Integration
Quality control, often abbreviated as QC, includes a range of activities and processes that focus on maintaining and improving the quality of products and services. It involves systematic checks, inspections, and tests at various stages of production, distribution, and delivery to identify and rectify defects or deviations from established standards. While quality control is integral to the manufacturing process, its significance extends far beyond the normal features.
In supply chain management, the concept of quality control is broader and more detailed. It involves the management and oversight of quality-related activities at every stage of the supply chain, from sourcing raw materials to the final delivery of products or services to customers. Quality control in supply chain management ensures that each component and process contributes to the overall quality and reliability of the end product or service.
7 Key Elements of Quality Control in Supply Chain Management
Supplier Qualification and Selection
The function of quality control in supply chain management lies in selecting and qualifying reliable suppliers. This process involves evaluating potential suppliers’ capabilities, track record, quality management systems, and adherence to regulatory standards. Choosing the right suppliers is critical to ensuring a consistent flow of high-quality materials and components.
Quality Standards and Specifications
Establishing clear quality standards and specifications is essential to aligning all supply chain stakeholders. These standards serve as a reference point for suppliers, manufacturers, and distributors, ensuring that everyone works toward the same quality goals. It also facilitates the identification of non-conforming products or materials.
Inbound Inspection and Testin
Quality control begins at the initial stage into the supply chain. Inbound inspection and testing involve assessing the quality of raw materials or components received from suppliers. Any discrepancies or defects are identified and addressed promptly, preventing defective or odd materials from entering the production process.
Process Control
Ensuring consistent quality throughout the manufacturing or service delivery process is vital. Process control measures, such as statistical process control (SPC) and lean manufacturing principles, help identify deviations and variances early, allowing for timely corrective actions.
Traceability and Documentation
Quality control in supply chain management necessitates meticulous record-keeping and traceability. This includes documenting each step of the production or service process, as well as the origin and history of materials and components. Such documentation facilitates recalls, audits, and compliance with regulations.
Supplier Audits
Periodic supplier audits are conducted to assess a supplier’s adherence to quality standards and contractual agreements. These audits help maintain supplier accountability and encourage continuous improvement in quality.
Inventory Management
Quality control extends to inventory management practices, ensuring that products are stored, handled, and transported in a manner that preserves their quality and integrity. This includes appropriate storage conditions, shelf-life monitoring, and inventory rotation.
Benefits of Quality Control in Supply Chain Management
The integration of quality control practices into supply chain management offers many benefits for organizations:
Enhanced Product Quality: A primary benefit is the consistent delivery of high-quality products or services, which builds trust with customers and minimizes the risk of costly recalls or returns.
Supply Chain Transparency: Quality control practices promote transparency within the supply chain. This transparency enhances communication among stakeholders, including suppliers, manufacturers, distributors, and customers. It fosters a collaborative environment that can lead to shared insights and improved decision-making.
Cost Reduction: Effective quality control helps identify and rectify defects early, reducing production waste, rework, and the overall cost of poor quality.
Supply Chain Resilience: Implementing quality control measures enhances supply chain resilience. When disruptions occur, such as natural disasters or unforeseen events, organizations with robust quality control mechanisms can adapt more effectively and minimize supply chain interruptions.
Market Expansion: High-quality products and services not only retain existing customers but also attract new ones. Organizations that consistently deliver superior quality are better positioned to expand into new markets and diversify their customer base.
Cost-efficient Return Management: In the event of product returns, efficient quality control practices facilitate seamless returns management. This process includes identifying the root cause of returns, implementing corrective actions, and ensuring that returned products are properly handled and disposed of.
Compliance and Risk Mitigation: Quality control ensures compliance with regulatory standards, reducing the risk of legal and reputational issues. It also enhances the organization’s ability to adapt to changing regulations. High-quality products are less likely to experience defects or issues, reducing the risk of costly recalls or returns. Recall incidents can result in significant financial losses, damage to brand reputation, and legal repercussions. Quality control acts as a preventive measure, identifying and rectifying potential issues before they escalate into larger problems.
Improved Supplier Relationships: Collaboration with suppliers on quality control fosters stronger, more reliable supplier relationships, leading to a more resilient supply chain.
Customer Satisfaction: Meeting or exceeding customer expectations in terms of quality enhances customer satisfaction, loyalty, and positive feedback.
Operational Efficiency: Process improvements and streamlined operations result in increased efficiency and competitiveness within the supply chain.
Competitive Advantage: Organizations that prioritize quality control in supply chain management gain a competitive edge by consistently delivering superior products and services.
Conclusion
Quality control is an indispensable component of supply chain management, handling every phase of the supply chain, from supplier qualification to final product delivery. The role of quality control is not confined to ensuring product quality but extends to cost reduction, risk mitigation, regulatory compliance, and overall operational excellence. Organizations that recognize the symbiotic relationship between quality control and supply chain management are better positioned to thrive in today’s complex and competitive business environment. As the supply chain landscape continues to evolve, quality control remains an important quality assessor in achieving and sustaining success.